Ressourcen sparen, Lieferketten sichern, Wettbewerbsfähigkeit stärken
Wie Hartmetallrecycling bei Bosch Schule macht
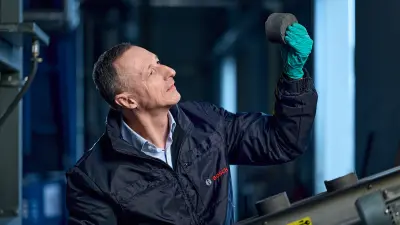
Ein ganz spezieller Rohstoffeinkäufer
Dietmar Burkhart macht seine Arbeit bei Bosch mit Herzblut, und das seit gut 30 Jahren. Der Diplom-Betriebswirt von der schwäbischen Alb in Süddeutschland arbeitete lange nahe seiner Heimat, in Reutlingen im Bereich Automobilelektronik, und wechselte dann zu Bosch in der Schweiz, wo er heute für den Geschäftsbereich Power Tools im Produktbereich Accessories als Rohstoffeinkäufer arbeitet. Er arbeitet mit Leidenschaft daran, Potenziale zu suchen, um die Wettbewerbsfähigkeit seines Geschäftsbereichs zu sichern. Dazu gehört vor allem, Kosten im Blick zu halten.
Burkhart erkannte vor mehr als einem Jahrzehnt das große Potenzial bei der Verwertung von Hartmetallwertstoffen. Diese entstehen zum Beispiel an Fertigungsstandorten des Geschäftsbereichs Power Tools, wo Sägeblätter hergestellt werden. Der Hauptstandort für dieses Produkt ist die italienische Stadt Udine, mit den Fertigungswerken in den nahegelegenen Gemeinden Martignacco und Fagagna.
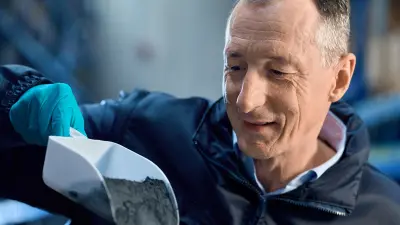
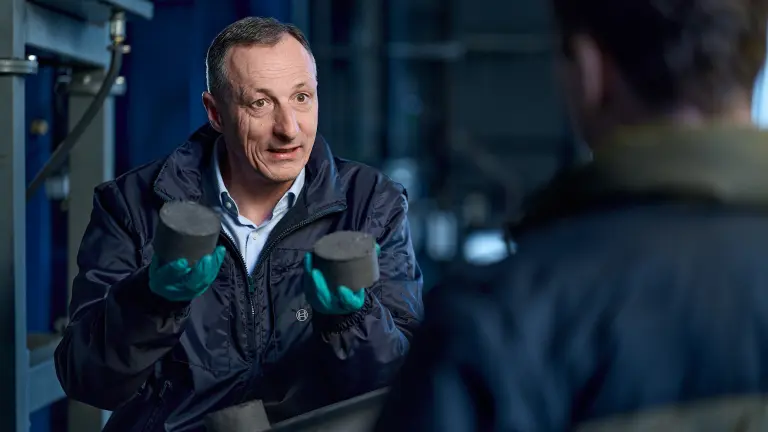
Das Laden des Videos setzt Ihre Zustimmung voraus. Wenn Sie durch Klick auf das Play-Symbol zustimmen, lädt das Video und es werden Daten an Google übertragen sowie Informationen durch Google auf Ihrem Gerät abgerufen und gespeichert. Google kann diese Daten bzw. Informationen gegebenenfalls mit bereits vorhandenen Daten verknüpfen.
Hartmetall ist nie Abfall
Im einen Werk, Martignacco, werden Hartmetallspitzen für Sägeblätter produziert. Das Hartmetallpulver wird in der benötigten Formgebung der Spitzen für die Sägeblätter gepresst und dann im Sinterofen gehärtet. Im anderen Werk Fagagna werden die Hartmetallspitzen dann auf die gefertigten Sägeblätter gelötet. Danach folgt ein Schleifprozess. Das Hartmetall ist ein Gemisch aus viel Wolframkarbid und etwas Kobalt, denn nur so sägt das Sägeblatt gut und lange. Aber was macht man mit dem, was beim Fertigungsprozess übrigbleibt? Das Material ist teuer. Deswegen sind die Reste, die bei der Herstellung vor allem durch Abrieb beim Schleifen übrigbleiben, viel zu schade, um sie wegzuwerfen.
Bislang, so erzählt Burkhart, wurden die Hartmetallreste an Wertstoffhändler verkauft. Der Wertstoffhändler verkaufte die Hartmetalle weiter, und nach einigen Stationen kaufte sie ein Spezialist zur Wiederaufbereitung auf. Bosch wiederum erwarb für die Produktion Hartmetallpulver von Pulverherstellern, unabhängig davon, ob es aus wiederaufbereitetem Material stammte oder als Primärrohstoff in einer Mine abgebaut worden war.
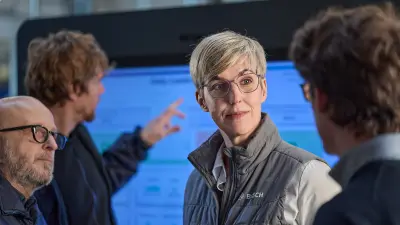
Aufbereiten und Wiederverwenden
An diesem Punkt setzte der gewiefte Schwabe vor rund zehn Jahren an: Hochwertiges recyclingfähiges Material nach dem Fertigungsprozess im Bosch-Werk nicht einfach für einen geringen Preis abzugeben, sondern in Eigenregie mit Partnerbetrieben für den erneuten Einsatz nutzbar zu machen.
So kam es zu der Initiative am Standort Udine, wie sie heute praktiziert wird. Bosch bereitet die beim Fertigungsprozess übrig gebliebenen Materialien bis zu einem gewissen Grad für das Recycling auf. Späne, Schleifschlamm und Pulver werden entölt und zu faustgroßen zylindrischen Pellets gepresst. Danach verkauft Bosch das Material einem Recycling-Spezialisten für einen festgelegten Preis. Nachdem der Dienstleister es wieder zu verwendbarem Rohstoff aufgearbeitet hat, kauft Bosch es zurück, um es dann erneut in den Fertigungsprozess einzubinden. Die andere Variante: Bosch gibt das Material kostenlos beim Dienstleister ab und bezahlt bei der Rücknahme des wieder fertigungstauglichen Materials nur den Recyclingprozess.
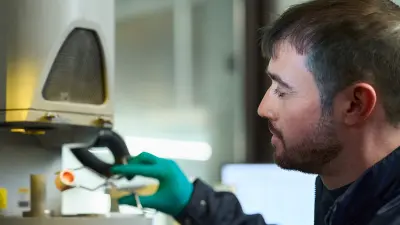
Einen Kreislaufprozess etablieren
Mit Michael Zeiher fand Burkhart einen der ersten Mitstreiter. Der Kollege aus dem internationalen Einkauf verfügte über Erfahrung mit dem Verkauf von Stoffen, die bei der Fertigung in Prozessen wie Sägen oder Schleifen in Bosch-Produktionsstätten anfallen, auch Hartmetallen. Zeiher war es, der die Türen für die international übergreifende Zusammenarbeit von Bosch-Standorten bei der Hartmetallverwertung öffnete. Bei ihm laufen die Informationen zusammen, an welchen Standorten welche Wertstoffe anfallen. Zeiher wusste, wo sich geeignete Hartmetalle beschaffen lassen, bei denen es sich lohnt, sie wieder in den Fertigungsprozess einzubinden. Gemeinsam mit Burkhart übernahm er die Aufgabe, den Ankauf der Wertstoffe für die Fertigung von Hartmetallprodukten bei Bosch Power Tools zu organisieren. Mittlerweile sind 20 Bosch-Standorte aus ganz Europa an der Initiative beteiligt.
Teamarbeit ist Trumpf
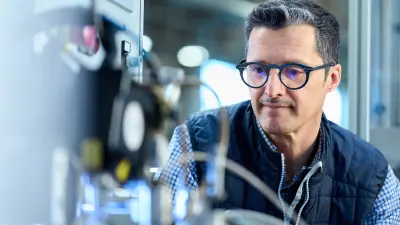
Ein Projekt erfolgreich umzusetzen, ist bei Bosch nie die Sache von Einzelkämpfern. Es müssen Menschen gefunden werden, die die Idee mittragen, weil sie von ihr überzeugt sind. Dazu gehören Profis in unterschiedlichen Gebieten – von der Forschung bis zur Fertigung. Piero Lupetin ist einer von ihnen. Er ist Teamleiter der Hartmetallentwicklung und Spezialist für Rohmaterialien in Udine, und muss dafür sorgen, dass das Hartmetallpulver die erforderliche Qualität für die Fertigung hat. Lupetin konnte sich überzeugen, dass das Verfahren, einen Recyclingprozess einzuführen, keinerlei negative Auswirkungen auf die Qualität des Rohstoffs und des Endprodukts hat. „In seiner Materialqualität ist das Hartmetallpulver aus Rezyklat auf dem Niveau des Materials, das aus der Mine gewonnen wird“, so Lupetin.
Von einer anderen Entscheidungsinstanz, der Produktentwicklung, musste das Projekt auch grünes Licht bekommen. Massimo Tolazzi, Entwicklungsleiter für das Endprodukt Sägeblätter, weiß, dass die Hartmetallspitzen auch mit dem neuen Verfahren zur Rohstoffnutzung die höchsten Anforderungen an die Produktqualität erfüllen. „Wir stellen damit sicher“, so Tolazzi, „dass sich Nutzerinnen und Nutzer bei Schnittqualität und Haltbarkeit unserer Produkte auf uns verlassen können.“
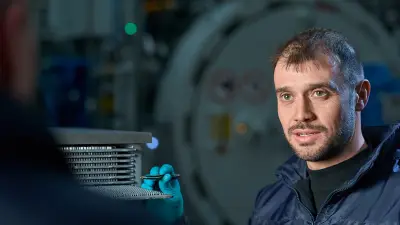
Ein neues Verfahren muss auch Rückhalt bei jenen finden, die dafür verantwortlich sind, dass alles, was ein Werk verlässt, den eigenen hohen Erwartungen an Qualität entspricht. Deswegen steht auch Martina Hinze hinter der Entscheidung, den Recyclingprozess bei der Hartmetallverarbeitung fest zu etablieren. Die Standortverantwortliche in Udine ist überzeugt, dass sich dieses Konzept kräftig weiterentwickeln wird. „Unsere Standorte Fagagna und Martignacco bei Udine stehen nicht nur für Hartmetallkompetenz, sondern nehmen im Fertigungsverbund von Bosch Power Tools beim Recycling hochwertiger Stoffe eine Pionierrolle ein. Mit unseren Erfahrungen können wir Wissen gewinnen, das sich auch in anderen Bereichen bei Bosch einsetzen lässt. Darauf sind wir hier in Udine stolz.“
Nachhaltigkeit und Lieferketten
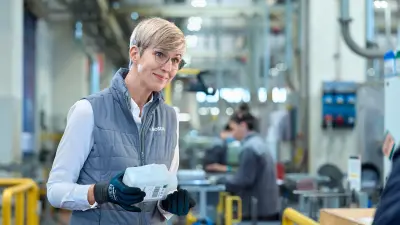
Diese Pionierrolle beschränkt sich aber nicht nur auf die Fertigungsanforderungen und Kostenreduzierung. Der neue Prozess ist auch im Sinne der Nachhaltigkeit ein wichtiger Schritt. Denn je mehr wiederverwendet werden kann, desto weniger neue Rohstoffe müssen abgebaut werden.
Doch es gibt noch einen dritten Grund, sich für dieses Projekt einzusetzen, wie Dietmar Burkhart berichtet: „Wir können mit unserem Ansatz zur Stärkung einer Kreislaufwirtschaft nicht nur ressourcenschonender arbeiten, indem wir wiederverwerten. Wir können auch unsere Lieferkettenresilienz verbessern.“ Je weniger Bosch auf dem freien Markt einkaufen muss, desto weniger abhängig ist das Unternehmen von den fragilen weltweiten Lieferketten. Das ist immer wieder eine Herausforderung. Bei der Blockade des Suez-Kanals wurde sichtbar, wie schnell bei Lieferketten eine kritische Situation entstehen kann.
Die erfreuliche Bilanz ist, dass zum Beispiel in Udine, wo dieses Projekt begann, mittlerweile schon 20 Prozent des angelieferten Hartmetallpulvers aus recycelten Materialien aus Bosch-Quellen stammen. Dazu trägt auch bei, dass sich zahlreiche Bosch-Standorte beteiligen und ihre Hartmetall-Wertstoffe in diese Kreislaufwirtschaft einfädeln.
„Unterscheiden“, so sagt Piero Lupetin, der Materialspezialist in Udine, „kann man Rohmaterial aus der Mine und das Sekundärmaterial aus der Aufarbeitung nicht.“ Denn beides, nicht nur das Rezyklat, durchläuft einen aufwändigen Prozess, um höchste Qualität für die Herstellung des Elektrowerkzeug-Zubehörs zu gewährleisten.
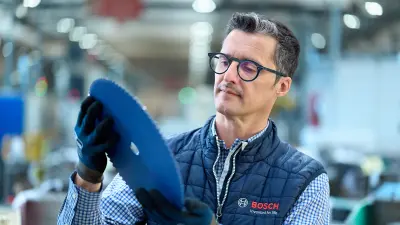
Kreislaufwirtschaft, auch über Bosch Power Tools hinaus
Die Perspektive für das Hartmetallrecycling bei Bosch ist, den Anteil von 20 Prozent zu verdoppeln. Das ist ein wichtiger Beitrag, um die Kreislaufwirtschaft weiter zu verstärken und die Lieferkettensicherheit zu erhöhen.
Aber dieses Projekt für Hartmetallrecycling ist kein Einzelfall. Im Rahmen seiner Strategie zur Kreislaufwirtschaft fokussiert Bosch sich auf drei Säulen: das Materialrecycling, aber auch Materialeffizienz und „Second Life“. Während Materialeffizienz das Reduzieren des Rohstoffeinsatzes meint, steht der Begriff Second Life für die Verlängerung des Produktlebens durch Wiederverwendung, Reparierbarkeit und Wiederaufarbeitung.
Das Projekt am Standort Udine ist ein wichtiger Meilenstein für die dritte Säule der Kreislaufwirtschaft, das Materialrecycling. Und dieses Pilotprojekt, das bereits 2013 startete, hat vielversprechende Perspektiven. Aus den heute beteiligten Standorten werden bald schon 30 geworden sein, und nicht nur von Bosch Power Tools. Auch andere Geschäftsbereiche mit Standorten in ganz Europa sind dabei.
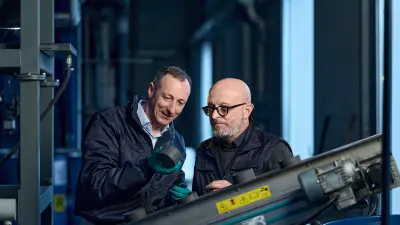