Extending machine lifespan with remanufacturing
Bosch Rexroth breathes new life into old machinery
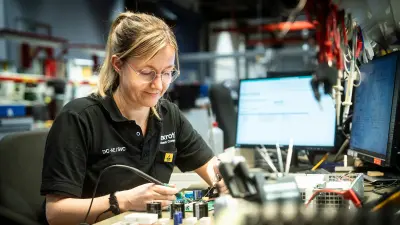
François Duquesne is happy: “Everything is just as it should be.” He casts a satisfied gaze over the machine next to him. Every second, it closes and seals cardboard boxes. In a next step, a robot arm sticks on delivery labels, one box after the other. “That’s just the way it should work.”
Duquesne, the general director of Normandise Pet Food in Vire, France, is standing in front of a large, silver-colored machine on the shopfloor. For 20 years, the machine has been packing and labeling pet food. Bosch Rexroth electronic drives ensure that the process runs automatically and smoothly. So that it stays that way, the machine in the plant in Normandy was refurbished last year.
As part of Bosch Rexroth’s remanufacturing service, used components are completely overhauled. As a drive and control technology specialist, Bosch Rexroth reprocesses the parts to original-equipment standard. At the customer’s, these “reman” parts are then reinstalled in the machinery. “Customers save up to 50 percent compared with a new product. And they get a materials warranty of two years, with an option of up to five years, just like with a new product,” says Daniel Voegeli, the head of services in Bosch Rexroth’s Automation unit. “During overhauls like this, the focus is on keeping manufacturing operations running, on compatibility with existing machinery, and on not having to buy any new machinery.”
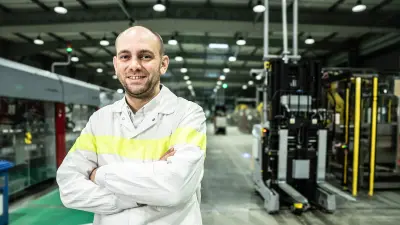
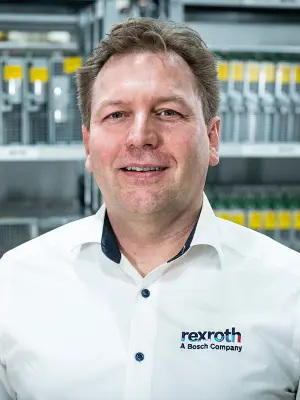
Reman products are quickly available worldwide.
Products’ carbon footprint
The decisive issue for remanufacturing customers is not only the cost saved and the reduction in effort. Duquesne also sees sustainability as the reason for working with Bosch Rexroth. “It’s a win-win situation for all concerned,” Voegeli says. He lists the environmental benefits: “Remanufactured components have half the carbon footprint of new products. As a rule, we can carry on using existing housings. And with every product, we conserve valuable resources, such as the rare earths used in magnets.”
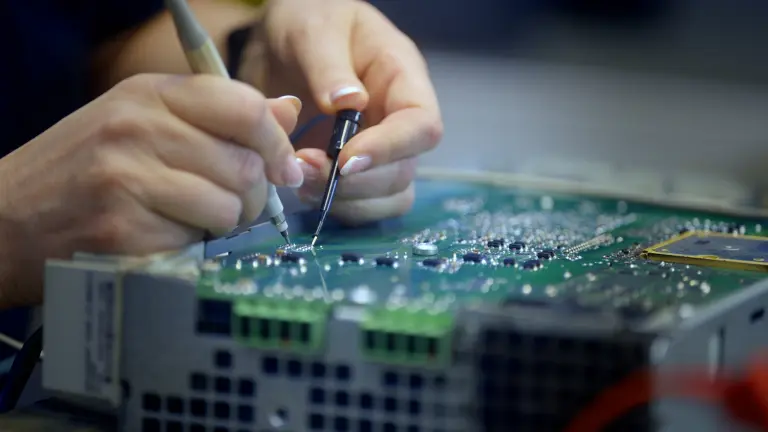
Loading the video requires your consent. If you agree by clicking on the Play icon, the video will load and data will be transmitted to Google as well as information will be accessed and stored by Google on your device. Google may be able to link these data or information with existing data.
In Vire, a total of 25 motors and drive units were given a general overhaul. “The machinery was working perfectly. Apart from the usual wear and tear, there was no reason to replace it,” Duquesne says. Together with his brother, he runs the family-owned company. Set up in 1991, it turns 150 tons of meat into wet dog and cat food every day. “Every hour a machine is out of action costs us roughly 8,000 euros,” the 36-year-old says as he makes his way through the packaging shop. “So the shorter and more foreseeable downtime is, the better it is for us.” In the remanufacturing process, total machine downtime when removing and installing parts is just 15 minutes. While Rexroth refurbishes the part, an identical spare ensures that the machine keeps running.
50 percent
cost saving compared with new part
The French packaging machinery company Jyga is also a firm proponent of this service. It supplied the packaging line in Normandy. It is installed in the 75,000 square-meter production shop, and is one of four Jyga lines operated by the pet-food producer Normandise Pet Food. “More and more customers are contacting us to ask about this subject. To save costs, while also avoiding production downtimes, they want to maximize the service life of their machinery,” says Yvan Reigner, sales account manager at Jyga. And this is where Bosch Rexroth comes in: as a manufacturer with decades of experience, the company knows exactly what components are at risk of breaking down after years of use, and can replace precisely those parts at the right time.
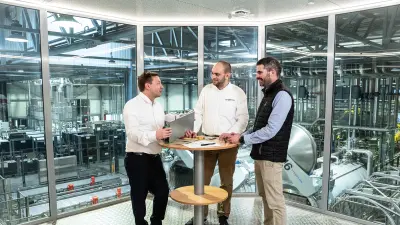
When usage data and the type of application are combined with this expertise, Bosch Rexroth can plan the overhaul together with the customer and carry it out professionally. “For us, collaboration with Bosch Rexroth fulfills two conditions. First, our customers are satisfied, since they get excellent quality for a very fair price. And second, working with Rexroth helps us pursue our own sustainability strategy for our service operations,” Reigner says.
Bosch Rexroth has been offering this service since 2004. Components that have been removed from machinery are sent to the company’s centers of competence, where they are refurbished. “We offer this service in Europe, North and South America, South Africa, India, and China. This means that Rexroth-quality reman products are quickly available worldwide,” Voegeli says. Once a component has been remanufactured, it is returned to the customer.
Voegeli explains that customer requirements were the origin of this service. After all, the operators of machinery can overhaul the mechanical workings of their lines, but restoring the original state of the automation electronics is something only the original manufacturer can do. “We saw those customers needed a solution here. The service we offer is now so standardized and industrialized that you cannot tell the difference between a new product and a completely overhauled one,” Voegeli says. Nowadays, the remanufacturing process generally takes a maximum of 13 days from collection to return — in urgent cases, remanufacturing can also be offered as a same-day service.
A business with a bright future
“We had a good nose early on. And the fact that reducing carbon footprint has been a central concern for companies like Jyga and Normandise Pet Food for some years now also has a positive impact on our business,” Voegeli says. Since it started offering its remanufacturing service, Bosch Rexroth has generated sales revenue of roughly half a billion euros. And over the next three to four years, the company expects to see annual sales growth of 10 percent.
One other reason remanufacturing is now especially in demand is that the service life of machinery is getting longer. “In many cases, it’s worth overhauling the drive components twice during service life,” the 51-year-old Voegeli says.
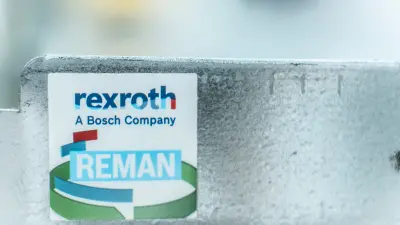
Remanufacturing as a service and a product
Bosch Rexroth is continuously expanding its reman portfolio. In addition to its on-the-spot service for customer machinery, the company has been buying up discarded and defective products since 2022. These are professionally overhauled and remarketed as reman products. Bosch Rexroth now offers more than 80 percent of its product portfolio as reman products.
“As long as we don’t run out of packaging materials, we can look forward to our machines running smoothly for the next 20 years — thanks to reman components,” Normandise Pet Foods’ François Duquesne says with a smile. Things are looking good for the year ahead: in 2025, new remanufacturing projects are planned for two other production machines at Normandise Pet Food that feature Rexroth parts.
Bosch-wide strategy: second life thanks to circular economy
For the Bosch Group divisions, there is a requirement that they enhance the sustainability of their products along their entire life cycle. This is part of the Bosch circular economy strategy. The aim is to reduce use of materials and products’ carbon footprint. In addition, the recycling of materials can especially avoid the risk attached to certain parts of the value chain, such as raw materials extraction. In the Bosch Group, the term “second life” relates to all measures for the reuse, repair, and recycling of products and components. And with its remanufacturing, Bosch Rexroth gives old drive and control products a second life. In other words, it achieves the goal of prolonging products’ and components’ service life.