Conserving resources, securing supply chains, improving competitiveness
Hard metal recycling sets a precedent at Bosch
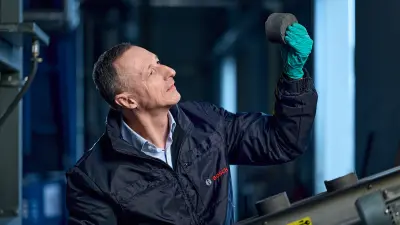
A raw materials buyer with a difference
For Dietmar Burkhart, working for Bosch has been a passion for nearly 30 years. After many years working for the Mobility Electronics division in Reutlingen, Germany, the business administration graduate and native of southwestern Germany moved to Bosch in Switzerland, where he now works as a raw materials buyer for the Power Tools division’s Accessories business unit. There, he devotes a great deal of energy to looking for potential ways of safeguarding his division’s competitiveness. Above all, this is about keeping an eye on costs.
More than a decade ago, he was struck by the huge potential that lies in recycling hard metal. These metal compounds are a byproduct at the Power Tools manufacturing sites that produce sawblades. The main location for this is the Italian city of Udine, with its manufacturing sites in the nearby municipalities of Martignacco and Fagagna.
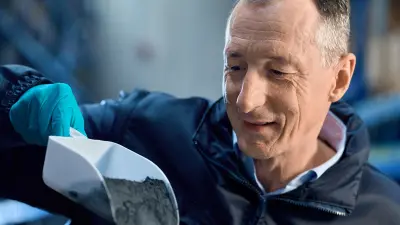
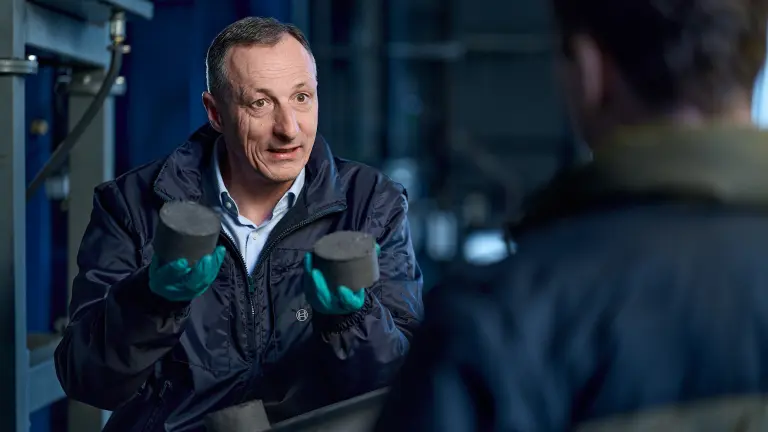
Loading the video requires your consent. If you agree by clicking on the Play icon, the video will load and data will be transmitted to Google as well as information will be accessed and stored by Google on your device. Google may be able to link these data or information with existing data.
Hard metal: too good to waste
At the Martignacco plant, the sawblades’ hard metal tips are produced. Hard metal powder is compressed and molded to form the tips, which are then hardened in a sintering furnace. At the Fagagna plant, the hard metal tips are soldered onto the finished sawblades. This is then followed by a grinding process. The hard metal is a compound of mainly tungsten carbide and a minor amount of cobalt, as only this will ensure the sawblades’ sharpness and long life. But what should be done with the metals left over from this process? They are expensive. Accordingly, the leftovers, which mainly arise as a result of grinding, are much too valuable to throw away.
Up to now, Burkhart says, the residual hard metal has been sold to recyclable dealers. These companies resell the hard metal, and after a number of stages a specialist recycling company buys them. For its own part, Bosch has purchased hard metal powder from powder producers regardless of whether they are the result of a recycling process or have been extracted by mining.
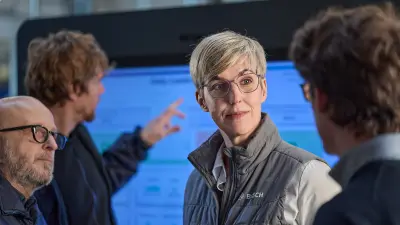
Reprocess and reuse
And roughly ten years ago, this got Dietmar Burkhart thinking. Instead of simply selling off valuable recyclable materials for a low price at the end of the manufacturing process in the Bosch plant, why couldn’t Bosch work with partners to make these materials reusable itself?
This was the start of the initiative that is now everyday practice at the Udine location. To a certain degree, Bosch reprocesses the materials left over in the manufacturing process to make them ready for recycling. Oil is removed from the shards, grinding sludge, and dust, which are then compressed to form fist-sized cylindrical pellets. Bosch then sells the materials to a recycling specialist for a fixed price. It buys them back once the service provider has processed them into a usable raw material that can be fed back into the manufacturing process. Alternatively, Bosch gives the service provider the materials free of charge and pays only for the recycling process when it takes the reusable materials back.
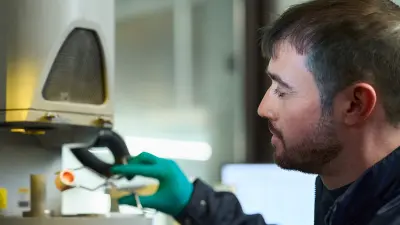
Setting up a circular process
Michael Zeiher was one of the first like-minded partners Burkhart found. Working in global purchasing, Zeiher had experience of selling the materials that arise in Bosch plants during processes such as sawing and grinding, including hard metal. It was Zeiher that opened the door for the international collaboration of Bosch locations in hard metal recycling. It is his job to know what recyclable materials have accumulated at what locations. Zeiher knew where to obtain suitable hard metal that was worth plowing back into the manufacturing process. Together with Burkhart, he assumed the task of organizing the purchase of materials for the manufacture of hard metal products at Bosch Power Tools. Twenty Bosch locations across Europe are now part of the project.
Teamwork makes all the difference
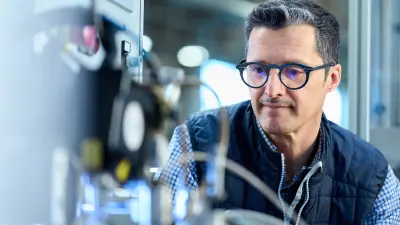
At Bosch, successfully implementing a project has never been a matter for lone wolves. Collaborators need to be found — people who believe in the idea and will help take it forward. This includes professionals in all kinds of fields, from research to manufacturing. Piero Lupetin is one such professional. In Udine, he is a section head for hard metal development and a raw materials specialist. It’s his job to ensure that the hard metal powder meets the requirements of manufacturing. Lupetin was convinced that the introduction of recycling would have absolutely no negative effects on the quality of either the raw material or the final product. “As a raw material, the recycled hard metal powder is just as good as freshly mined metal,” Lupetin says.
The project also had to be given the green light by another decision-making area — product development. Massimo Tolazzi, the head of engineering for sawblades, knows that the hard metal tips meet the highest product-quality standards, even with the new method of raw-materials use. “With it,” he says, “we ensure that users can rely on our products’ cutting quality and durability.”
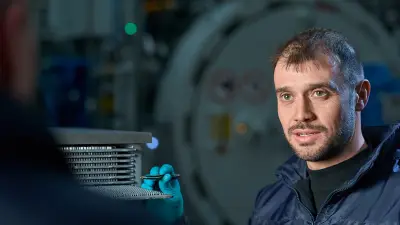
A new process also has to gain the support of the people who are responsible for ensuring the everything that leaves a plant meets its own high quality standards. Martina Hinze is such a person. The decision to make recycling a firm part of hard metal processing has her unqualified support. As the person responsible for the Udine location, she firmly believes that this concept has a strong future. “Our Fagagna and Martignacco sites are not only a byword for hard metal competence, but also play a pioneering role in the recycling of valuable materials within the Bosch Power Tools manufacturing network. Our experience is the basis of knowledge that can be used in other Bosch divisions as well. That’s something we in Udine are proud of.”
Sustainability and supply chains
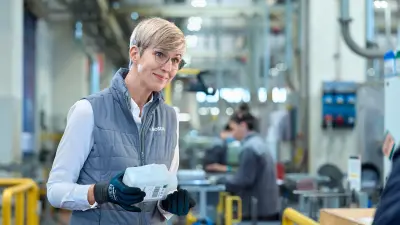
This pioneering role is not only limited to manufacturing requirements and to reducing costs. The new process is also significant from the point of view of sustainability. After all, the more that can be reused, the less need there is to extract raw materials.
And there’s a third reason to embrace this project, Dietmar Burkhart says: “With our approach for an improved circular economy, we not only conserve more resources through recycling. We also improve our supply-chain resilience.” The less Bosch has to procure on the open market, the less dependent it will be on fragile global supply chains. This is a constant challenge. The blockage of the Suez Canal showed how quickly supply chains can become critical.
The bottom line is encouraging. In Udine, for example, where the project began, 20 percent of the hard metal powder delivered comes from materials recycled by Bosch. This is helped by the fact that many Bosch locations are involved, feeding their hard metal into this circular economy.
As Udine’s materials specialist Piero Lupetin says, “You can’t tell the difference between raw materials straight from the mine and the secondary recycled materials.” This is because both types of material, not just the recycled ones, are examined thoroughly in order to ensure the highest quality for the manufacture of power-tool accessories.
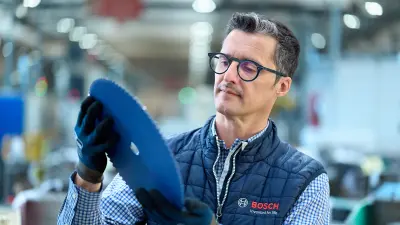
A circular economy beyond Bosch Power Tools
In the long run, Bosch wants to double the recycled hard metal 20 percent share. This will significantly help further strengthen the circular economy and supply-chain security.
But this project for hard metal recycling is not a one-off. As part of its circular-economy strategy, Bosch focuses on three pillars – materials recycling, materials efficiency, and “second life.” While materials efficiency is about reducing the amount of raw materials used, “second life” is about prolonging product life through reuse, repairability, and recycling.
The Udine project is an important milestone for materials recycling, the third pillar. And this pilot project, which started back in 2013, has a promising future. There will soon be 30 locations involved, and not just ones belonging to Bosch Power Tools: Other divisions with locations across Europe are also involved.
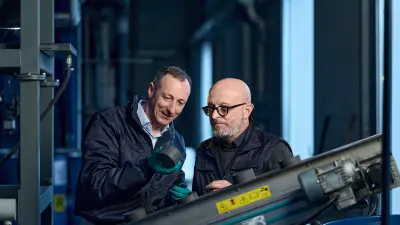